Maintaining key ice cream machine parts like the beater motor, thermostat, compressor, gaskets, and dispensing nozzles can save your business by preventing costly breakdowns and ensuring consistent quality. Regular upkeep reduces downtime, extends equipment lifespan, and keeps your products perfect. Staying on top of these components helps you avoid surprises and customer complaints. Want to keep your machine running smoothly and your business thriving? Continue on for expert tips to protect your investment.
Key Takeaways
- Regular maintenance of critical components like the beater motor and compressor prevents costly breakdowns and extends machine lifespan.
- Proper calibration of thermostats ensures consistent product quality, reducing waste and customer complaints.
- Routine inspection and cleaning of gaskets, seals, and nozzles prevent leaks, contamination, and operational clogs.
- Early detection of issues through monitoring helps avoid unplanned downtime and expensive repairs.
- Consistent preventative care enhances efficiency, reduces waste, and safeguards your business’s reputation and profitability.
The Importance of the Beater Motor and How to Keep It Running

The beater motor is essential for the ice cream machine’s performance because it powers the mixing paddle that creates smooth, evenly frozen ice cream. If the beater motor isn’t functioning properly, your ice cream’s consistency suffers, becoming too soft or icy. To keep it running smoothly, regularly check for signs of wear or overheating. Lubricate the motor if needed, and ensure it’s clean and free of debris. Avoid overloading the machine, as excessive strain can damage the motor. Using the correct settings and not forcing the machine helps prolong its life. A well-maintained beater motor guarantees consistent mixing, which directly impacts the quality of your ice cream. Proper care ensures your machine operates efficiently and consistently produces high-quality frozen treats. Monitoring motor performance and addressing issues promptly can prevent costly repairs and downtime. Additionally, paying attention to vibrations can help detect early signs of motor problems before they lead to failure. Regular maintenance of the machine components, including the beater motor, is crucial for long-term durability and optimal operation. Incorporating tuning techniques can also enhance the machine’s overall efficiency and lifespan. Keeping an eye on operating temperature is also important, as excessive heat can accelerate wear on the motor components.
Monitoring and Replacing the Thermostat for Optimal Performance
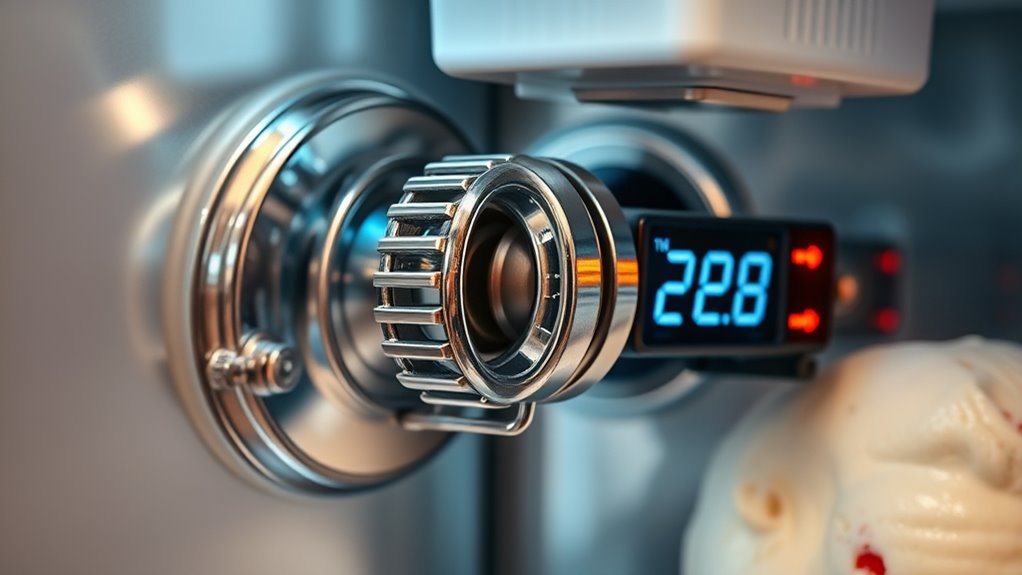
To keep your ice cream machine running smoothly, you need to regularly monitor the thermostat, which controls the freezing process. Proper thermostat calibration ensures it maintains the correct temperature, preventing unwanted temperature fluctuation that can compromise product quality. Check the thermostat’s readings frequently and compare them with a reliable thermometer. If you notice inconsistent temperatures or the unit isn’t freezing properly, it’s time to replace or recalibrate the thermostat. A faulty thermostat can cause your machine to overfreeze or underfreeze, leading to spoilage or poor texture. Regular maintenance and timely replacement help maintain ideal performance, extend your equipment’s lifespan, and ensure your ice cream stays perfect every time. Incorporating advanced HVAC technology can further optimize temperature control and improve overall efficiency. Additionally, implementing regular filter replacement practices ensures your refrigeration system operates efficiently, reducing energy costs and preventing potential breakdowns. Paying close attention to thermostat calibration is essential for consistent product quality and operational success. Staying vigilant with thermostat care is key to a successful business.
Common Issues With the Compressor and When to Repair or Replace
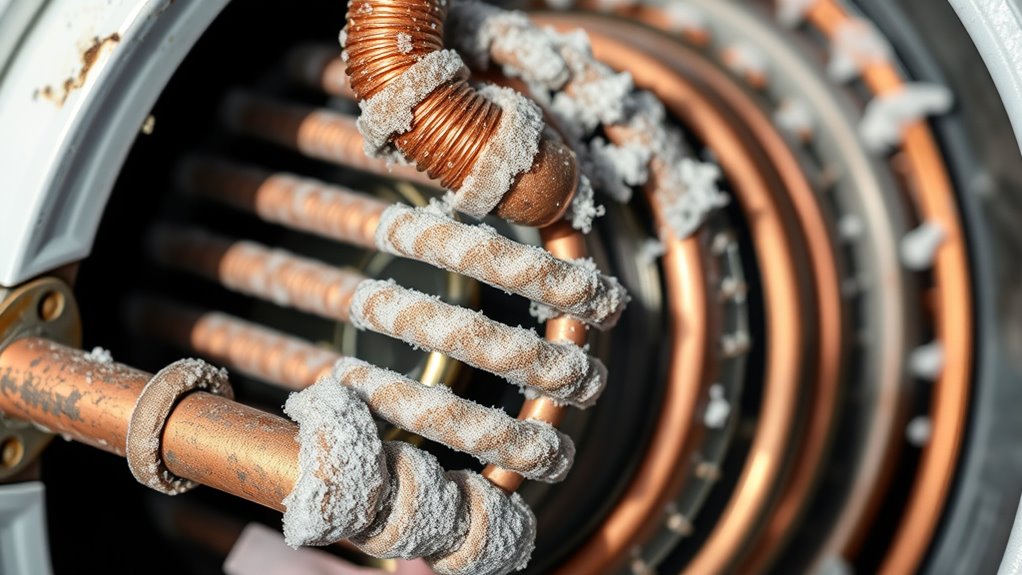
Compressor issues are a common cause of ice cream machine malfunctions, and recognizing the signs early can prevent costly repairs. If you notice unusual compressor noise, like grinding or banging sounds, it’s a sign something’s wrong. These noises often indicate worn bearings or motor issues that need attention. Additionally, refrigerant leaks can cause your compressor to work harder or fail altogether. Look for oily spots or ice buildup around the compressor area; these are signs of leaks. If you detect refrigerant leaks or persistent loud noises, it’s time to repair or replace the compressor. Ignoring these issues can lead to complete system failure, costly repairs, or even replacing the entire machine. Regular maintenance helps catch problems early and keeps your ice cream machine running smoothly. Proper maintenance is essential to ensure the longevity and optimal performance of your compressor and overall equipment. Incorporating energy monitoring features can also help identify inefficiencies early, potentially preventing compressor failure. Understanding compressor technology and how it affects performance can help you make informed decisions about repairs and replacements. Staying informed about Honda Tuning concepts can also inspire upgrades that improve your equipment’s efficiency, especially in systems that rely on compressors for optimal operation. Additionally, utilizing remote diagnostics can streamline troubleshooting and reduce downtime by enabling experts to assess issues without being physically present.
The Role of Gaskets and Seals in Preventing Leaks and Contamination
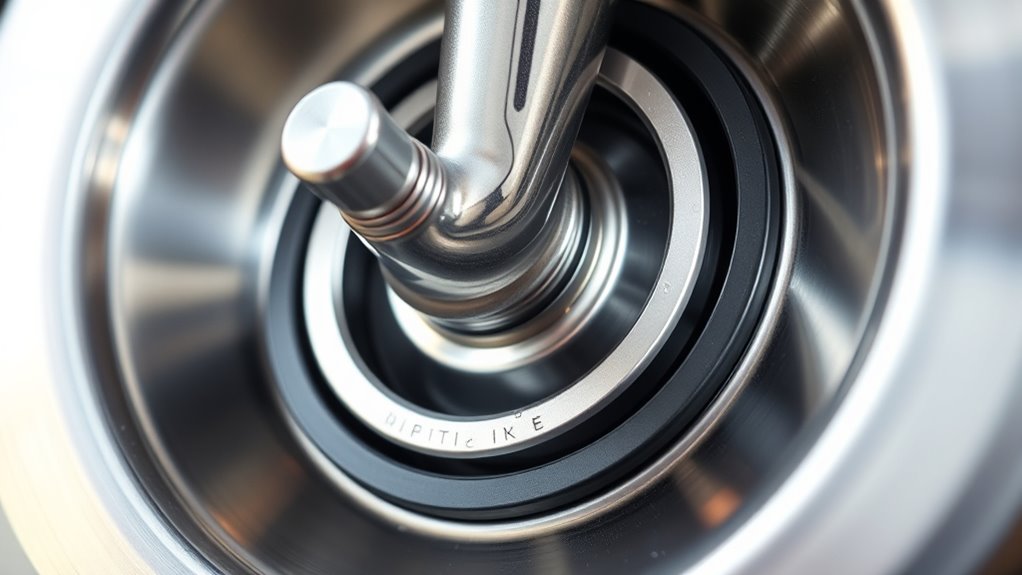
Gaskets and seals play an essential role in keeping your ice cream machine functioning properly by preventing leaks and contamination. The gasket material you choose directly impacts seal integrity, ensuring a tight fit that stops liquids or air from escaping. High-quality gasket materials, like rubber or silicone, resist wear, heat, and cold, maintaining a secure barrier over time. When seal integrity is compromised, leaks can occur, leading to contamination risks and potential machine damage. Regularly inspecting and replacing worn gaskets and seals helps preserve the machine’s performance and hygiene standards. Proper installation is also crucial to ensure a secure seal and prevent potential issues. Additionally, understanding gasket compatibility with your specific machine model can help improve longevity and effectiveness. Selecting the right gasket material based on material properties can significantly enhance durability and performance. Proper sealing is crucial for safe, efficient operation, and maintaining preventive maintenance routines can extend the lifespan of your equipment. By prioritizing the right gasket material and ensuring proper installation, you keep your machine running smoothly, reduce downtime, and protect your product quality. Implementing regular inspection routines can further identify early signs of wear and prevent costly repairs. Proper sealing is crucial for safe, efficient operation.
Regular Maintenance of the Dispensing Valve and Nozzle System
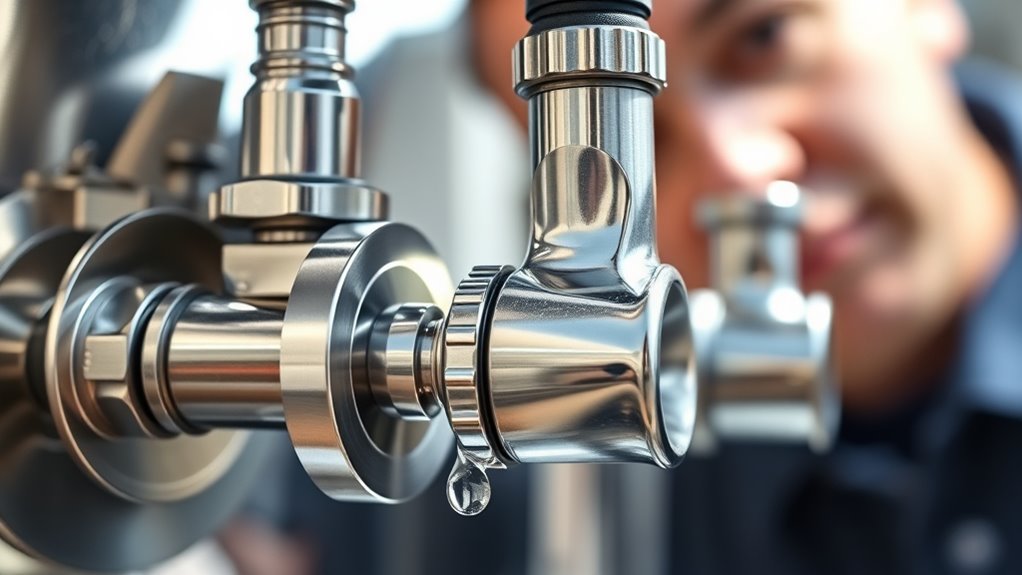
How often do you check and clean your dispensing valve and nozzle system? Regular maintenance is key to preventing clogs and ensuring smooth operation. Follow proper cleaning procedures by disassembling the parts and thoroughly sanitizing each component to remove residue and buildup. This helps sustain ice cream quality and reduces contamination risks. Additionally, regularly perform calibration techniques to ensure the dispensing system delivers the correct portion size and flow rate. Accurate calibration prevents waste and customer dissatisfaction. Keep a maintenance schedule and document each step to track performance. Regularly inspecting your cookie management settings can also help ensure optimal operation and security. Incorporating tuning techniques from Mazda vehicles can inspire innovative approaches to maintaining and optimizing your dispensing equipment. Applying preventative care principles from airless paint sprayers can also enhance the longevity of your machinery. Practicing system resilience by maintaining equipment for long-term resilience can provide valuable insights into preventative care. By maintaining the dispensing valve and nozzle system diligently, you extend its lifespan, improve product consistency, and avoid costly repairs. Consistent upkeep ultimately safeguards your business’s reputation and profitability.
Frequently Asked Questions
How Can I Identify if My Ice Cream Machine Parts Are Counterfeit?
To identify if your ice cream machine parts are counterfeit, start with counterfeit detection techniques. Check for inconsistencies in packaging, logos, or serial numbers. Genuine parts usually have clear markings and high-quality materials. Compare the parts to official manufacturer images. If something seems off or you can’t verify authenticity, contact the supplier or manufacturer directly. Using genuine parts guarantees safety, durability, and peak performance, protecting your business from costly failures.
Are There Eco-Friendly Alternatives for Replacing Common Machine Components?
Think of eco-friendly replacements as a breath of fresh air for your machine. You can swap out common parts with biodegradable lubricants and recycled metal components, which reduce environmental impact. These alternatives not only keep your equipment running smoothly but also help your business stay green. Choosing sustainable options guarantees you’re doing your part in protecting the planet while maintaining peak performance. It’s a win-win for your operation and the environment.
What Training Is Recommended for Staff to Maintain Machine Parts Effectively?
You should prioritize thorough staff training on machine maintenance to keep your equipment running smoothly. Focus on teaching your team proper cleaning, lubrication, and part replacement techniques, emphasizing eco-friendly practices when possible. Regular training sessions help staff stay updated on maintenance procedures and troubleshoot issues quickly. This proactive approach minimizes downtime, extends machine lifespan, and ensures consistent product quality, ultimately benefiting your business and customer satisfaction.
How Do Different Climates Affect the Longevity of Ice Cream Machine Parts?
Ever wondered how climate impact affects your machine’s part durability? Warmer, humid environments accelerate wear and corrosion, shortening the lifespan of critical parts. Conversely, cold, dry climates can cause materials to become brittle. You need to take into account your local climate when maintaining your equipment, ensuring proper storage and timely replacements. By understanding these climate impacts, you can better protect your investment and extend your ice cream machine’s longevity.
Can Upgrading Parts Improve Energy Efficiency and Reduce Operational Costs?
Upgrading parts can notably improve your ice cream machine’s energy efficiency and cut operational costs. With smart equipment upgrades, you’ll experience better energy savings because newer components often run more efficiently and require less power. This means lower utility bills and reduced wear on your machine. By investing in quality parts, you optimize performance, save money, and extend your equipment’s lifespan, making it a smart move for your business’s long-term success.
Conclusion
Remember, a stitch in time saves nine. By keeping your ice cream machine parts like the beater motor, thermostat, compressor, gaskets, and nozzles well-maintained, you prevent costly repairs and keep your business running smoothly. Regular checks and timely replacements ensure top-quality treats for your customers. Don’t wait for a breakdown—stay proactive and safeguard your investment. After all, an ounce of prevention is worth a pound of cure!